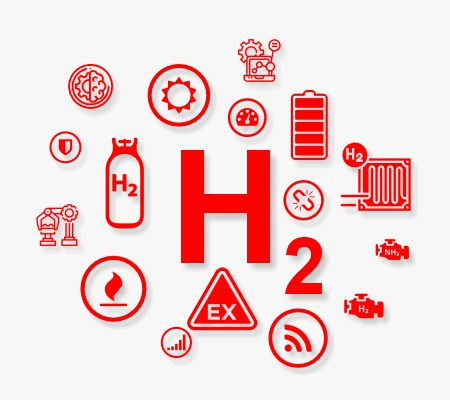
Specific requirements for hydrogen - H2
Our services around hydrogen vehicles mainly concern:
- Tanks by verifying UNECE R134 requirements with, in particular, burst tests, ambient cycling, drop (impact), surface damage, chemical exposure (+ ambient cycle), static pressure at high temperature, pressure cycles at extreme temperatures, residual pressure, residual burst resistance, fire resistance. .. Tests during which the tanks do not contain hydrogen
- Fuel cells and associated elements with the traditional set of automotive qualification tests performed but for which electromagnetic compatibility and thermal environment tests are performed while being supplied with hydrogen
H2 - Testing and servicing under control
H2 tank tests according to UN ECE R134 regulation
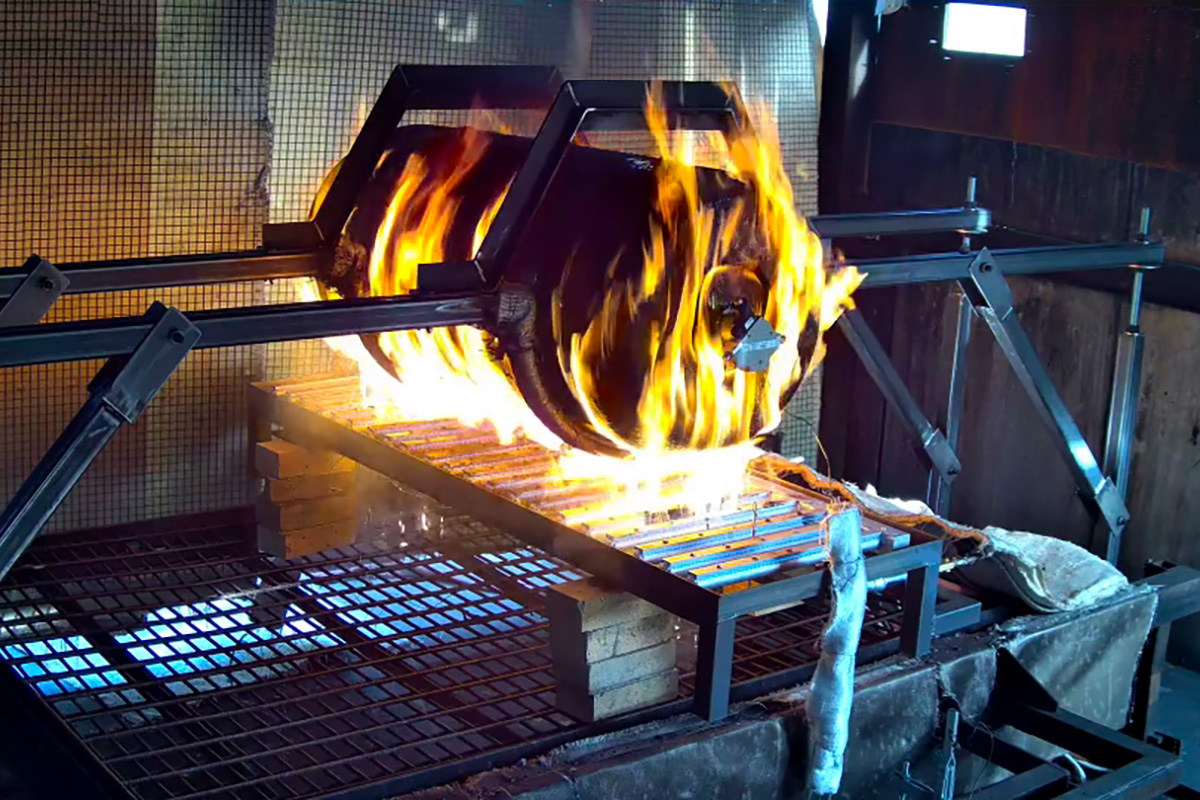
The tests are carried out on type IV hydrogen tanks in accordance with the requirements of regulation 134 (ECE R134).
Our benches are sized to qualify tanks from 20 to 255 liters in volume and used at the nominal pressure of 700 bars.
Nature of services provided
Test to verify measured reference characteristics
- Reference initial burst pressure
- Number of cycles of initial reference pressure
Test to verify durability of characteristics (hydraulic tests in sequence)
- Proof pressure testing
- Drop testing (shock)
- Surface damage
- Exposure testing to chemical agents and pressure cycles at room temperature
- High-temperature static pressure testing
- Pressure cycling at extreme temperatures
- Residual pressure testing
- Residual burst strength testing
Test to verify the characteristics expected for road use (pneumatic tests in sequence)
- Proof pressure testing
- Pressure cycles at ambient and extreme temperatures (pneumatic testing)*
- Leak/permeation tests under static pressure, at extreme temperatures (pneumatic tests)*
- Residual pressure test
- Residual burst strength test (hydraulic test)
*Feasibility study in progress
Fire resistance verification test (service shrinkage conditions)
An H2 servitude package to qualify your fuel cells
As part of manufacturer qualification, equipment under test (EST) must be tested in operation.
Our test centers dedicated to hydrogen-powered equipment are equipped with dedicated servitudes.
In the example of fuel cells, our test centers are equipped with hydrogen storage systems and have dedicated facilities (H2 power supply, gas extraction pods, H2 detectors, dedicated safeties...) for testing with the cell in operation.
- in electromagnetic compatibility
- in climatic environment
For other test typologies, our facilities enable us to check that the EST is working properly after the test sequence.
We offer you the design and development of a nacelle dedicated to your fuel cell distributing the fluids and cables required for its operation), the provision of the charging bay sized according to the fuel cell's power, the design and development of the control bay driving the cell, the chiller.
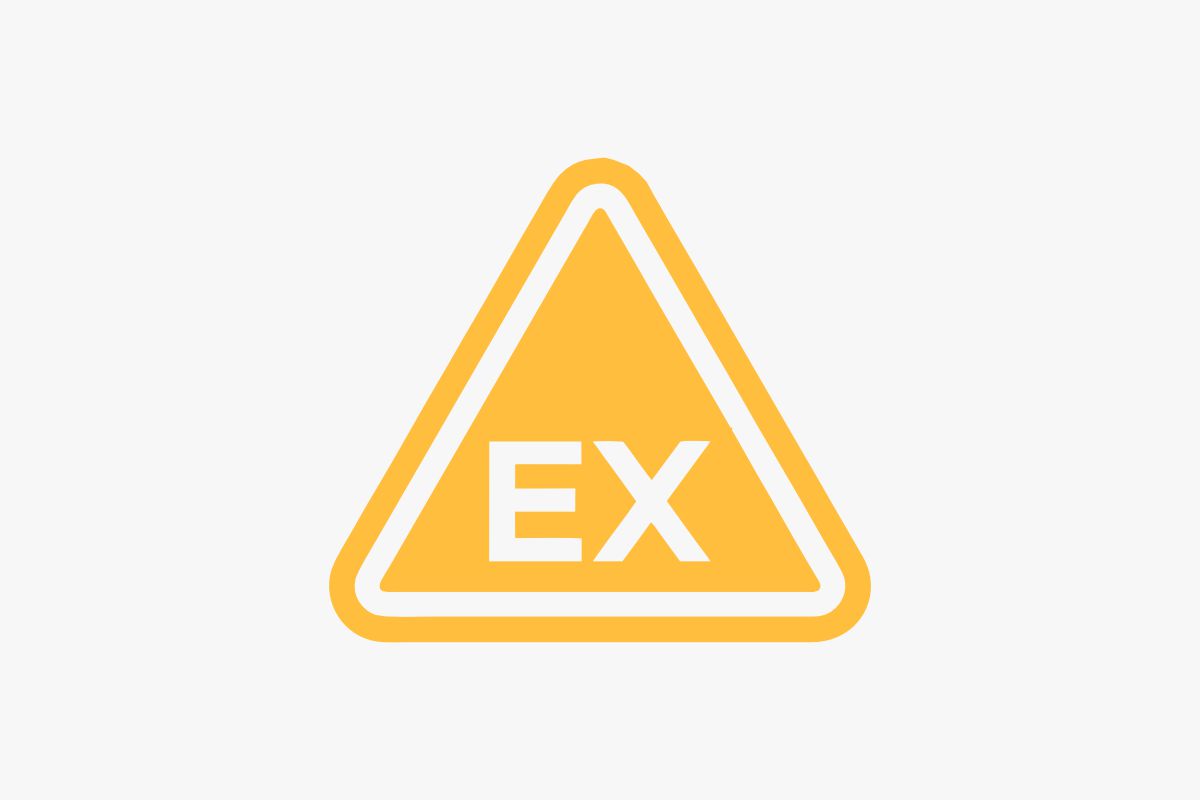
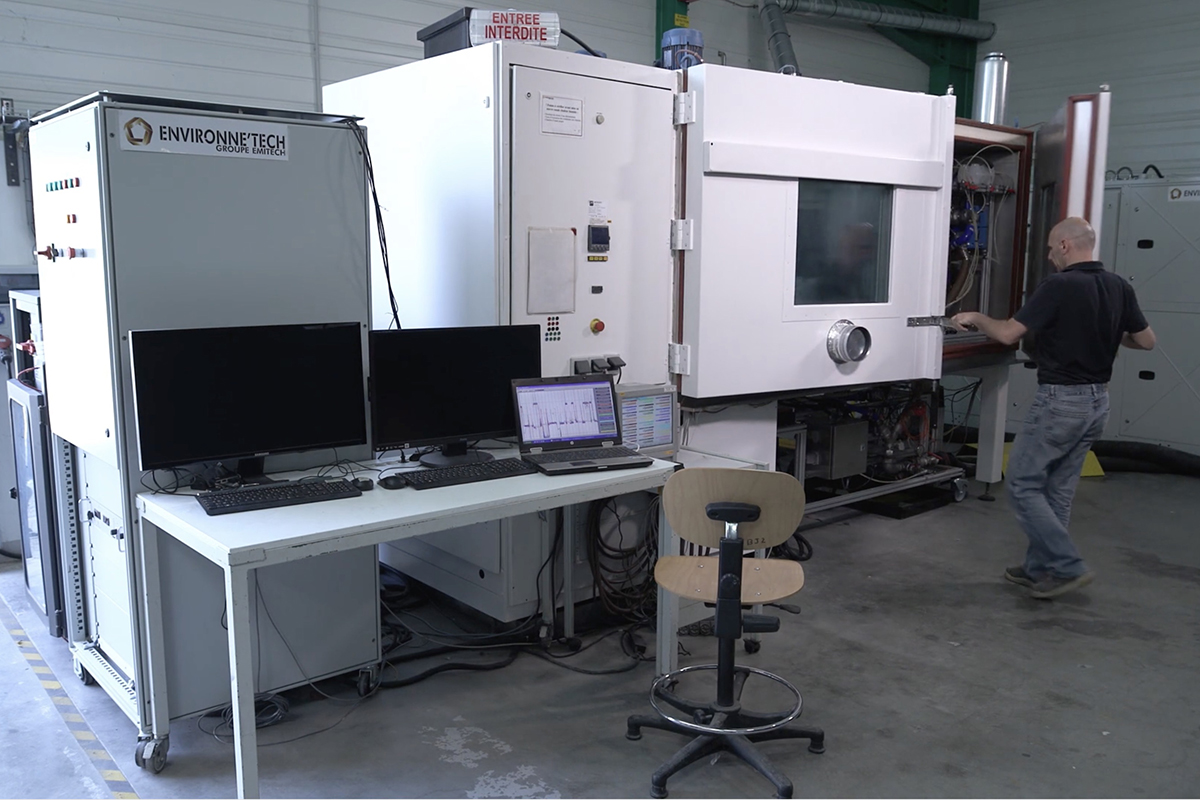
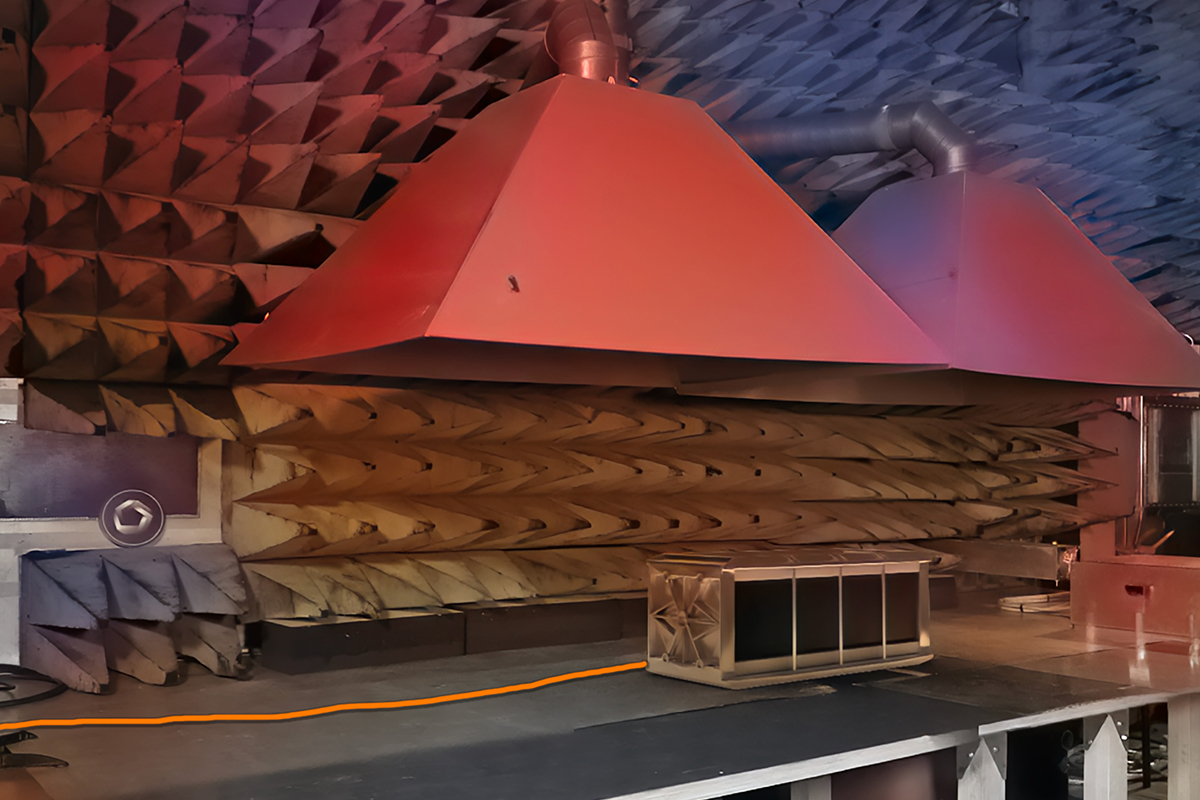
ICE H2 / NH3 engine development and validation
Our high-dynamic H2/NH3 engine test bench is the result of an adaptation of our high-performance test bench designed to meet engine development requirements for different types of engine: gasoline, diesel and natural gas (280 bar supply). It offers great versatility to address all engine development issues:
- Measurement and calibration optimization work on stabilized points for performance, combustion, consumption, pollutant emissions, etc.
- Automatic calibration
- Automatic conduct of experimental designs and associated data analysis
- Realization of standardized cycles under chassis dynamometer simulation conditions
- Simulation of customer-representative high-dynamic driving cycles (RDE)
- Accelerated engine maceration
- ECU software bypass prototyping
Our bench offers the option of operating in liquid NH3 mode (PFI or DI injection up to 100 bar) or gaseous NH3 (with a nominal flow rate of 150kg/h), but also in mixed NH3 + H2 combustion and H2 alone (nominal flow rate 25kg/h and nominal pressure of 40 bar)